Our Story
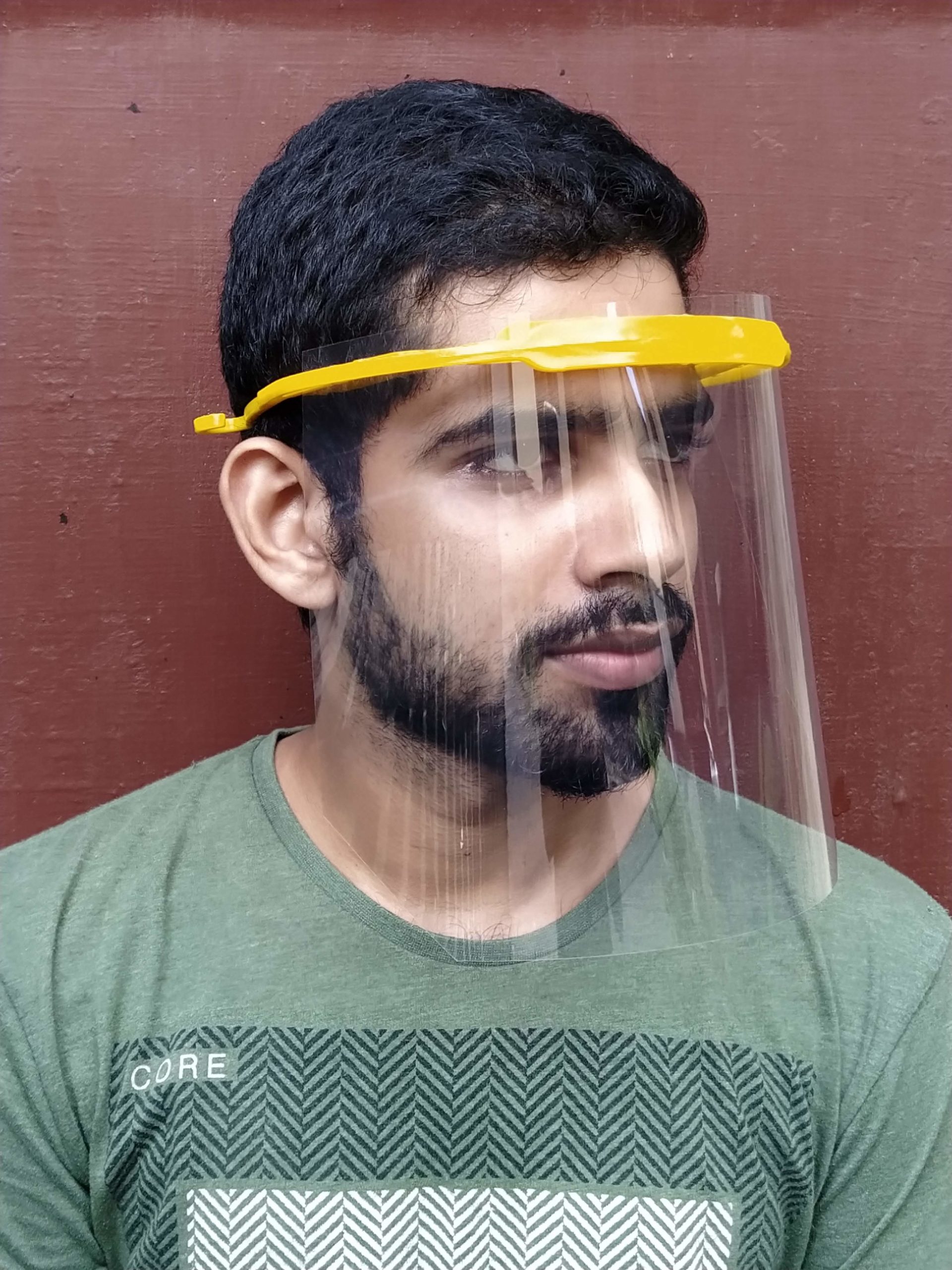
Hey, I am Mathew Varghese, Managing partner of veil healthcare solutions. I am an electronics engineer, who is also interested in extending my horizon by exploring other fields of engineering.
In my first year of college, I along with my friend built a 3D printer, which was like black magic at the time. I used to tinker with the 3d printer and co-founded a rapid prototyping service startup named Mak3rspace (https://mak3rspace.com) with my friend. We made enough pocket money from it and also won many awards for the work.
We graduated in 2019 and I decided to take a gap year to explore life after college. Meanwhile, I applied to colleges in the USA for robotics, AI, and Systems Engineering and subsequently got into the University of Michigan, University of Maryland, and Monash University. Then the corona hit and I found myself in a difficult situation with uncertainty in college admissions. I was freelancing at that time, and I started voluntarily 3d printing face shields for local healthcare workers. Soon I found that I have a shortage in PLA filament, which is the raw material for 3D printing. At that time, some of my friends were talking with the Pathanamthitta collector, Nooh IAS, and got access to a large stash of 3d printer PLA filament. Together, we supplied more than 5000 face shields by 3d printing. I thought publicity is cheap and defeats the purpose of the donation, and hence I didn’t post my efforts in social media, but I could never be more wrong. There was a shortage of PPE kits and I could’ve helped more people at the time of need.
Although I was too scared of the corona to go out, one day, my craving to eat jalebi forced me to go to a nearby bakery, and I wore the shield I made. The bakery owner enquired about it and I gave him one on the next day. Even he too got inquiries and he asked for more face shields. That’s when I started charging for them. More than 100 face shields got sold off in a few days. That’s when he proposed an idea of mass-producing the face shields by plastic molding. Although I was deterred by the initial cost, soon I found that it is a practical approach. I noticed that face shields were being imported from China and decided to start a production plant in Kerala. I teamed up with my buddy Aravind and two of my friends, Vaishnavi and Gauri, and formed a partnership. Gauri’s father has a plastic molding company and we made use of the facility to mold plastic.
We found the team to be strong, as everyone had some important skills to bring to the table. We designed the face shield, rapidly iterated using our 3d printers in 3 days, tested the market using the prototype models, and prepared the die from a local die manufacturing unit. We pooled in resources and registered the partnership, applied for PAN, Bank account, and GST, and started sourcing the components.
The single biggest hurdle we faced was sourcing the PET sheets required for making the shields. For that, Indiamart proved to be our life savior. We searched for the local market for PET sheets, but they were nowhere to be found. Eventually, sellers from all over India were charted and got some people who can deliver to Kerala. Meanwhile, we got orders by word of mouth and we were in business. Now, we are trying to scale up the business, while helping people to better protect themselves from the pandemic we are going through. Now, for the story to go on, I need to get more people to use this face shield and decrease the chance of contracting corona.